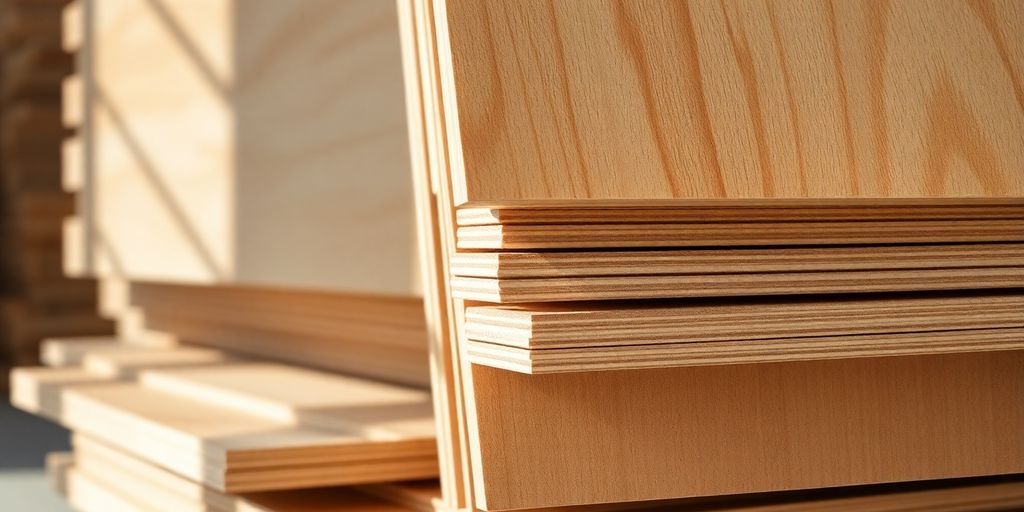
Tips for a Solid Subfloor
Understanding Plywood Subfloor Options
Types of Plywood for Subflooring
Okay, so you're thinking about plywood for your subfloor? Smart move! But hold on, not all plywood is created equal. You've got your CDX plywood, which is like the standard, economical choice. It's okay for subflooring, but don't expect a super smooth finish. Then there's stuff like Baltic Birch, which is a higher-end option. It's more durable and has a smoother surface. Basically, the type of plywood you pick depends on what you're planning to put on top of it. If you're doing tile, you might need something different than if you're laying carpet. Make sure to check the flooring trends before you make a decision.
Benefits of Plywood Subflooring
Plywood is a popular choice for subfloors, and for good reason. It's strong, stable, and relatively easy to work with. Plus, it's usually more affordable than some of the alternatives. Here's a quick rundown:
Strength: Plywood can handle a lot of weight without warping.
Stability: It resists shrinking and expanding with changes in humidity.
Ease of Installation: Most contractors know how to install plywood, and it doesn't require special tools.
Plywood subflooring offers a solid base for various types of finished flooring, including carpet, laminates, bamboo, and hardwood. It's a versatile option that can be used in both residential and commercial settings.
Common Uses for Plywood Subfloors
So, where does plywood really shine? Well, it's used in a bunch of places. Obviously, it's a subfloor, meaning it goes under your finished floor. But it can also be used as underlayment, which is an extra layer between the subfloor and the finished floor. Some people even use plywood as the finished floor itself! You can cut it into planks or shapes and lay them out however you want. Just make sure you seal it properly. Plywood subflooring is suitable for most types of flooring and provides an excellent base for tiles, hardwood floor installation, or carpeting.
Key Factors in Selecting Plywood Subfloor
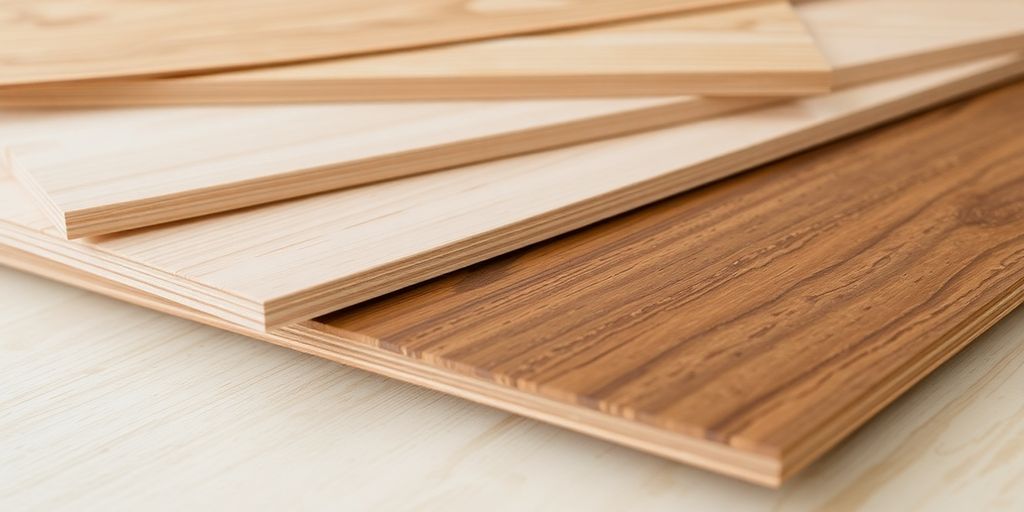
Choosing the right plywood for your subfloor is a big deal. It's not just about grabbing the cheapest stuff at the hardware store. You've got to think about a few things to make sure your floors are solid and last. Let's break down the key considerations.
Moisture Resistance Considerations
Okay, so moisture is the enemy. Plywood and water don't mix well, unless you're talking about specific types. The level of moisture resistance you need depends on where you're putting the subfloor. For bathrooms or kitchens, you'll want something that can handle humidity and spills. Regular plywood can warp or even rot if it gets too wet. Look for plywood that's treated or designed for moisture-prone areas. Also, think about your local climate. If you live somewhere humid, it's even more important to choose wisely.
Thickness and Strength Requirements
Thickness matters. A thicker subfloor is generally stronger and less likely to flex or sag. But how thick should you go? It depends on the spacing of your floor joists and the type of flooring you plan to install on top. Check local building codes for minimum thickness requirements. You don't want to end up with a bouncy floor, or worse, one that can't support the weight of your furniture. Here's a quick guide:
Floor Joist Spacing: Closer joists need less thickness.
Flooring Type: Tile needs a stiffer subfloor than carpet.
Load: Consider the weight of furniture and foot traffic.
Cost and Budget Considerations
Let's be real, budget is always a factor. Plywood prices can vary a lot depending on the type, grade, and thickness. CDX plywood is often the cheapest, but it might not be the best choice for every situation. Think about balancing cost with performance. It might be worth spending a bit more upfront to get a better quality plywood that will last longer and prevent problems down the road. Don't forget to factor in the cost of fasteners, adhesives, and any treatments you might need to apply. You can transform your home with expert hardwood floor installation services, but it's important to budget appropriately.
It's tempting to save money by going with the cheapest plywood, but remember that your subfloor is the foundation for everything else. Skimping here could lead to costly repairs later on. Consider it an investment in the long-term stability of your home.
Installation Techniques for Plywood Subfloor
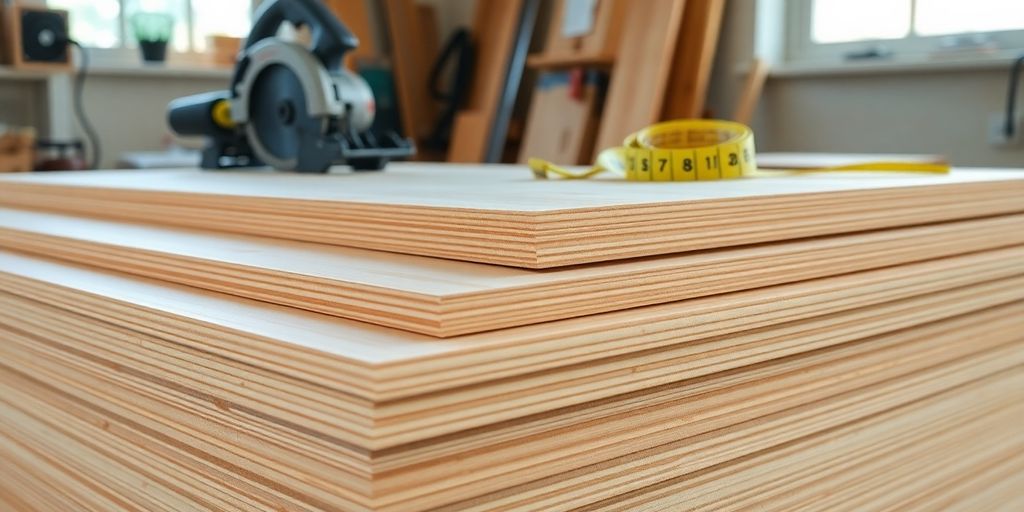
Preparation Steps for Installation
Okay, so you're ready to put down that plywood subfloor. First things first: prep work. This isn't the fun part, but trust me, skipping steps here will come back to haunt you. You need to make sure the joists are in good shape. Are they level? If not, you'll need to shim them. Seriously, don't skip this. Also, check for any signs of moisture or rot. Fix that before you even think about laying down plywood. Sweep, vacuum, do whatever it takes to get the area clean. You don't want any debris trapped under the plywood. Finally, let the plywood acclimate to the room for a few days before installing. This helps prevent warping later on.
Proper preparation is like laying the foundation for a house. If it's not solid, everything else will suffer.
Here's a quick checklist:
Inspect and repair joists.
Level the floor.
Clean the subfloor thoroughly.
Acclimate the plywood.
DIY vs. Professional Installation
Alright, so you've prepped the area, and now you're staring at a stack of plywood, wondering if you can really do this yourself. DIY installation can save you some serious cash, but it's not for everyone. If you're comfortable with power tools, know how to measure accurately, and aren't afraid of a little hard work, then go for it. However, if you're unsure about any of those things, hiring a pro might be the better option. Professionals have the experience and tools to get the job done quickly and correctly. Plus, they can handle any unexpected problems that might arise. Pioneer Concepts LLC offers hardwood flooring services that might be a good fit if you're feeling overwhelmed.
Here's a quick comparison:
FeatureDIYProfessionalCostLowerHigherTimeLongerShorterSkill RequiredModerate to HighHighRisk of MistakesHigherLowerToolsYou provideThey provide
Common Mistakes to Avoid
Okay, let's talk about some common pitfalls. First, using the wrong type of fasteners. Make sure you're using screws or nails that are designed for subfloor installation. Second, not staggering the seams. This is crucial for creating a strong, stable subfloor. Third, leaving too little or too much space between the plywood sheets. You need a small gap to allow for expansion and contraction, but too much space can create weak spots. Fourth, ignoring moisture issues. I can't stress this enough: moisture is the enemy of plywood. Finally, rushing the job. Take your time, double-check your measurements, and don't cut corners. Trust me, you'll be glad you did. Here are some mistakes to avoid:
Using incorrect fasteners.
Failing to stagger seams.
Ignoring moisture problems.
Rushing the installation.
Not accounting for expansion gaps.
Maintenance Tips for Plywood Subfloor
Regular Cleaning Practices
Okay, so you've got your plywood subfloor installed. Now what? Well, just like any other surface in your house, it's gonna need some cleaning. But don't just grab any old cleaner and go to town. You gotta be a little careful with plywood.
Sweep or vacuum regularly: This gets rid of the loose dirt and debris that can scratch the surface over time. I usually do this once a week, but if you have pets or kids, you might need to do it more often.
Damp mop carefully: When you mop, make sure the mop is damp, not soaking wet. Too much water can seep into the plywood and cause it to warp or swell. Use a mild soap solution – nothing too harsh.
Avoid abrasive cleaners: These can damage the finish on your plywood. Stick to gentle cleaners specifically designed for wood surfaces.
Moisture Control Strategies
Moisture is the enemy of plywood. Seriously, it can wreak havoc on your subfloor if you're not careful. Here's how to keep the moisture at bay:
Address leaks immediately: If you have a leak, fix it ASAP. Don't let water sit on the plywood for any length of time. This is super important.
Use a dehumidifier: In damp areas, a dehumidifier can help keep the moisture levels down. I run one in my basement during the summer months.
Ensure proper ventilation: Make sure your crawl space or basement is well-ventilated. This helps prevent moisture buildup. Check your vents regularly to make sure they aren't blocked.
Preventing moisture issues is way easier than dealing with the aftermath. Take the time to inspect your subfloor regularly and address any potential problems before they become major headaches.
Repairing Damage to Plywood Subfloor
Even with the best care, your plywood subfloor might get damaged at some point. Here's how to handle some common problems:
Small cracks: For small cracks, you can use wood filler to patch them up. Sand the area smooth after the filler dries.
Soft spots: Soft spots usually indicate water damage. You'll need to cut out the damaged section and replace it with new plywood. Make sure to address the source of the moisture before you do the repair.
Delamination: If the layers of the plywood are separating, you'll need to replace the affected section. There's really no way to fix delamination once it starts. Consider water damage repair if you suspect moisture is the cause.
| Type of Damage | Repair Method | Notes all the same. I'm not sure if that makes sense, but I hope it does!
Comparing Plywood Subfloor to Other Materials
Plywood vs. Oriented Strand Board (OSB)
Okay, so you're trying to figure out what to use for your subfloor, and it's down to plywood versus OSB (Oriented Strand Board). Both are engineered wood products, but they have some key differences. Plywood is made of layers of wood veneer glued together, while OSB is made of wood strands compressed and glued.
Here's a quick rundown:
Cost: OSB is generally cheaper than plywood. If you're on a tight budget, that's a big plus.
Moisture Resistance: OSB can be more prone to swelling when it gets wet compared to some types of plywood. However, some OSB is treated for better moisture resistance.
Strength: Plywood tends to be a bit more rigid and resistant to bending over long spans. But OSB is no slouch either, and it's often used in wall and roof sheathing.
Installation: Both are pretty easy to work with, using standard tools. Plywood can sometimes be easier to nail into, depending on the density of the OSB.
Ultimately, the choice depends on your specific needs and budget. If you're in a high-moisture area, consider treated OSB or a higher grade of plywood. If you need maximum rigidity, plywood might be the better bet. If you are looking for affordable flooring options, OSB might be the way to go.
Plywood vs. Concrete Subfloors
Now, let's talk about plywood versus concrete. Concrete subfloors are common in basements or in slab-on-grade construction. They're super solid, but they're also very different from plywood.
Moisture: Concrete can wick moisture from the ground, so you need a moisture barrier. Plywood, while not waterproof, is less likely to have moisture issues if properly installed with a vapor barrier.
Installation: Installing flooring over concrete requires different techniques. You might need to use adhesives, self-leveling compounds, or create a sleeper system to attach the flooring. Plywood is nailed or screwed directly to joists.
Comfort: Concrete is cold and hard. Plywood provides a bit of give and warmth underfoot.
Cost: Concrete is usually part of the original construction, so it's not really an
Environmental Considerations for Plywood Subfloor
Sustainability of Plywood Materials
Okay, so when we talk about plywood and the environment, it's not all doom and gloom. Plywood can actually be a pretty decent choice if you think about where it comes from. A lot of manufacturers are getting better at using sustainable forestry practices. This means they're replanting trees and managing forests responsibly. If you're trying to be eco-conscious, look for plywood that's certified by the Forest Stewardship Council (FSC). This certification tells you the wood was sourced in a way that protects forests and the people who depend on them. Choosing ply for flooring is a great option if you’re looking to reduce your environmental footprint.
Recycling and Disposal Options
What happens when your plywood subfloor reaches the end of its life? Well, recycling plywood isn't as straightforward as tossing a plastic bottle into the bin. Because it's made of layers of wood glued together, it's harder to break down. However, there are still options. Some construction and demolition recycling centers will accept plywood. Also, consider hardwood floor repairs to extend the life of your existing subfloor. You can also repurpose old plywood for other projects, like making furniture or shelving. If you absolutely have to dispose of it, check with your local waste management to see if they have any specific guidelines or programs for wood waste.
Impact on Indoor Air Quality
This is where things get a little tricky. Plywood is made with adhesives, and some of those adhesives can release volatile organic compounds (VOCs) into the air. VOCs can cause health problems, so it's something to be aware of. The good news is that there are low-VOC plywood options available. Look for plywood that's labeled as "CARB compliant" or "ULEF" (ultra-low emitting formaldehyde). These types of plywood have been tested and certified to meet strict emissions standards. Also, make sure your space is well-ventilated, especially after installation. This helps to dissipate any VOCs that might be released. Consider flooring trends that prioritize low-emission materials for better indoor air quality.
It's important to remember that choosing environmentally friendly plywood is a step in the right direction, but it's not a perfect solution. Like any building material, plywood has an environmental impact. By making informed choices and considering the full lifecycle of the product, you can minimize that impact and create a healthier home.
Choosing the Right Plywood Grade
Understanding Plywood Grades
Plywood grades are like report cards for wood, telling you about its quality and what it's best used for. The grading system usually uses letters, like A, B, C, and D, with A being the highest quality and D being the lowest. These grades are based on the appearance and number of defects on the wood's surface. It's important to know what these grades mean so you don't end up with plywood that's not right for your project. For example, if you're doing something where the wood will be visible, like a cabinet, you'll want a higher grade like A or B. But if it's going to be hidden, like under a floor, you can save money by using a lower grade like C or D.
Selecting the Best Grade for Your Project
Choosing the right plywood grade really depends on what you're building. Think about what you need the plywood to do. Is it going to be holding a lot of weight? Will it be exposed to moisture? Will people see it? If you need something strong, look for structural grades. If moisture is a concern, go for marine-grade or exterior-grade plywood. And if you want it to look nice, pick a higher grade with a smooth surface. It's also a good idea to check local building codes to make sure you're using the right grade for your project. If you're refinishing hardwood floors hardwood floor refinishing, you'll want to make sure the subfloor is in good shape, and the right plywood grade is key to that.
Impact of Grade on Performance
The grade of plywood affects how well it performs in different situations. Higher grades are stronger and more resistant to moisture, which means they'll last longer and won't warp or rot as easily. Lower grades might be cheaper, but they're also more likely to have problems like knots, voids, and uneven surfaces. This can make them harder to work with and less reliable over time. So, while it might be tempting to save money by using a lower grade, it could end up costing you more in the long run if you have to replace it sooner. Here's a quick rundown:
A Grade: Best for visible surfaces, minimal defects.
B Grade: Good for painting or staining, few defects.
C Grade: Suitable for hidden areas, some defects.
D Grade: For structural use only, many defects.
Using the correct plywood grade is not just about aesthetics; it's about ensuring the safety and longevity of your project. Always consider the specific requirements of your build before making a decision.
When picking plywood, it's important to choose the right grade for your project. Different grades have different qualities, which can affect how your finished work looks and lasts. For example, higher grades are smoother and have fewer knots, making them great for visible areas. If you're unsure about which grade to select, visit our website for more tips and guidance!
Wrapping It Up
Choosing the right plywood subfloor can feel overwhelming, but it doesn't have to be. Take your time to think about your specific needs, like moisture levels and the type of flooring you plan to install. Remember, not all plywood is created equal, so look for quality options that fit your budget. Whether you're going for a DIY project or hiring a pro, make sure you understand what you're getting into. In the end, a solid subfloor will set the stage for a beautiful and lasting floor in your home. Good luck with your renovation!